We have had a lot of questions about what we do at ReBlade, so here’s a quick summary of how we managed a recent turbine blade decommissioning project.
Project Background
We were contacted by a utility scale owner/operator who had three damaged blades in need of disposal. Sometimes blades become damaged during construction, sometimes during operation but it’s not something that happens often. Turbine blades are made of tough stuff.
Blades are inert waste, and they do not decompose. This means that the blades we were asked to deal with had been lying on site for some time. While this is not ideal from a circular repurposing point of view, these blades had tremendous value in terms of helping to refine decommissioning handling protocols for future whole site decommissioning.
Our clients are taking the responsible approach by investing in sustainable disposal. Circular decommissioning isn’t the cheapest solution for turbine blades, but it is the best solution. Right now it’s helping to refine blade handling processes and enabling skills development.
It’s also helping to determine resource levels for planning whole site decommissioning.
When it comes to whole site decommissioning there are big opportunities to localise the workforce, and identifying – in detail – the skills and operational approaches required is essential. So, by working with us now, our clients are directly investing in creating a sustainable future for turbine blade decommissioning.
Blade Decommissioning Project Planning
This turbine blade decommissioning project started with project specification and planning.
Our approach is always determined by the condition of the blades, the needs of the site and the repurposing potential. We talked through all the options with our client then agreed the course of action that best met their priorities.
We visited the site, reviewed how the blade had been stored and assessed the blade condition.
This is a key step in our method because the condition of the blade determines both how we’ll manage it on-site, and the potential for a circular end-destination.
Next up, we liaised with the site manager, we undertook a risk assessment and created a method statement, outlining our operational activities in detail. All this was agreed at a very early stage.
As the client had asked us to make blade derived items from these blades we then jointly progressed ideas into designs.
With all the project planning stages delivered and agreed, we agreed a suitable date for blade removal and scheduled in our team and the plant required to carry out the work.
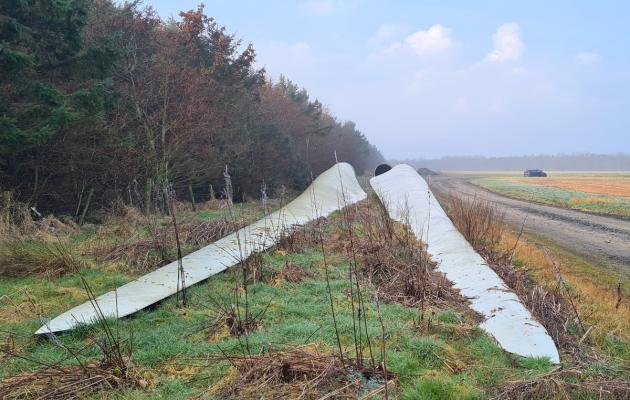
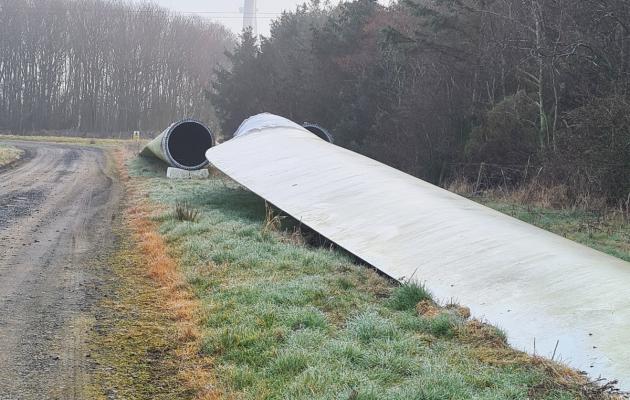

On-Site Blade Management & Clean-Up
After arriving on-site the very first thing our team did was to cordon-off a defined work area, which was agreed in advance. Turbine blades are HUGE. Our team needs space to manoeuvre them, as well as space for the plant we use to downsize and move the blades.
Before we started the on-site works, the risk assessment for the project was reviewed again, and any localised changes were noted.
Using careful lifting and moving techniques, which were agreed in advance, we moved the blades in a way that protected their structural integrity. All downsizing, lifting and moving techniques are designed to protect their circular economy potential.
We worked on one blade at a time, and an important stage of this process was when the blade was lifted. At this point we assessed the blade condition once again, paying particular attention to any water ingress and, as the blade had been lying on the ground, we carefully assessed the underside condition.
This on-site review informed the cutting strategy. The blades were then carefully cut, loaded and strapped, ready for transportation.
Any loose fibres or site disturbances were made right. The designated site work area was then cleaned, reinstated. All plant vehicles left site, and the cordon was removed
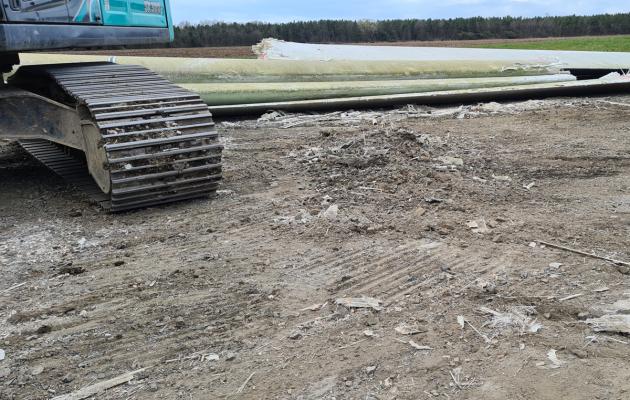
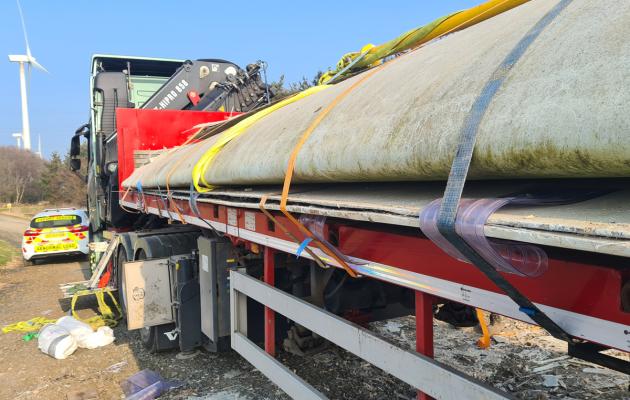

Blade Transport & Workshop
The cut segments of blades were transported to our storage yard and workshop, and then each segment was assessed and graded – both internal and external condition assessments.
At this stage, the end use for each blade segment has generally still to be determined. The blades could assist in fibre recovery projects, they could provide seating for families in parks, they could become the roof of a bicycle park or they could be used for a bridge or walkway.
We avoid landfilling blade material. Some of the blades, particularly those in a very poor condition, will be shredded down. This shredded material has a value too, sometimes being used by researchers to help inform pyrolysis development or fibre recovery technology.
But where the blade is in reasonably good condition, as in this particular project, we use our understanding of blades to design a useful second life for them. Our approach to product design is that if you can make it from wood, you can make it from a blade – albeit that a turbine blade is a LOT more challenging to work with than wood!
Designs will continue to be created, technical feasibility undertaken and, as I type, the blades are being turned into the specified end uses. We will update this blog with examples of the completed items once they’re ready.
Sustainable Blade Decommissioning
So, that's a quick snapshot of how we recently dealt with a request from a client to sustainably dispose of three 40 metre wind turbine blades.
While ReBlade is currently scaling up for large scale whole site decommissioning projects we also decommission and sustainably dispose of blades, nacelles and hubs on a small scale across Europe. We view each project - regardless of numbers or size - as vitally important. Every project helps refine our operations, and will directly inform cost-effective decommissioning for our clients while helping to minimise waste going to landfill, as and when the first generation of wind farms are decommissioned and / or repowered.
There’s a lot of talk within the industry about potential solutions for blade waste. Our clients are directly addressing the imminent need for solutions by tasking us with sustainable disposal now so that we are ready, with tried and tested processes in place, for us to decommission the blades on a site by site basis along circular principles.